The electric vehicle (EV) market has undergone a radical transformation over the past three decades, largely driven by the ongoing reduction in lithium-ion battery costs.
Global average prices fell from $153 per kilowatt-hour (kWh) in 2022 to $149 in 2023, and Goldman Sachs Research projects they will drop to $111 by the end of this year.
Their researchers forecast that average prices could fall towards $80 per kWh by 2026, representing a nearly 50% decline compared to 2023.
This leads to a scenario where electric vehicles could reach cost parity with petrol cars in terms of total ownership costs without relying on subsidies.
But how has this come about?
The decline in battery prices is due to several key factors.
First, economies of scale in production have increased as demand for electric cars has grown, especially in Europe, where decarbonisation goals and incentive policies have played a fundamental role.
Additionally, improvements in manufacturing processes and advancements in material technology have optimised efficiency and reduced costs per unit of energy.
Goldman Sachs’ report particularly highlights two crucial aspects: technological innovation and decreasing metal costs for battery production.
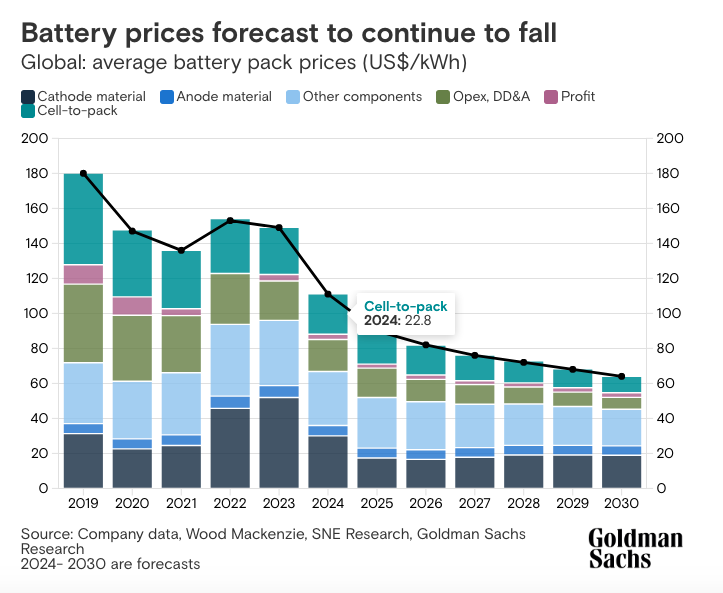
Focusing on the first point, the report notes:
“We’re seeing the release of multiple new battery products with around 30% higher energy density and lower costs.”
Innovation is tied to product structure, and now battery cells are becoming larger.
Typically, many cells are placed in smaller modules, which are then combined into a larger battery pack.
Now, there is a trend to eliminate modules and go straight from cells to packs.
“This helps save space inside. In this way, costs are reduced with simpler structures, while battery energy is increased at the same time,” states the document published by Goldman Sachs.
The second factor cited is the continued decline in metal prices for batteries, including lithium and cobalt.
This aspect is significant, as almost 60% of the total cost of these products comes from metals.
From 2023 to 2030, over 40% of the decline is expected to result solely from lower raw material costs, due to the high “green inflation” recorded between 2020 and 2023.
Price levels were very high back then.
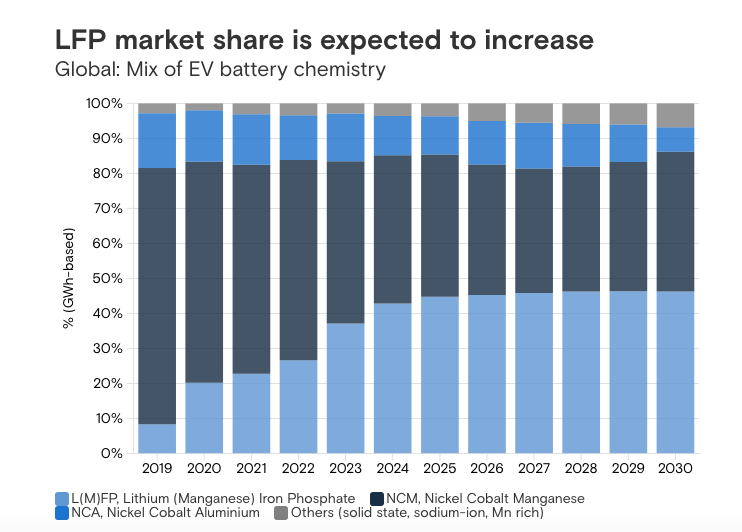
Projections and challenges for battery production in Europe
Despite these positive aspects, it is important to note that the European battery market faces major challenges in its expansion.
According to a report by Meticulous Research, investments are expected to exceed $415.9 billion in the coming years, with a compound annual growth rate (CAGR) of 33.1% up to 2031.
This growth is largely driven by government policies aimed at reducing battery prices and promoting investment in local production.
However, reliance on international supply chains, especially for raw materials like lithium, poses a significant risk.
Geopolitical tensions between global powers such as China and the United States, along with rapid technological advances in Asia, have raised concerns about supply chain stability.
In this context, Michel Bayings, a management consultant at Emobility Consulting, emphasises that “investments are directly linked to stable political environments with clear objectives,” highlighting the need for a favourable setting to attract sustainable investments.
Eastern Europe: An emerging focus for battery production
In response to growing demand, countries like Hungary and Poland have emerged as battery production hubs.
These nations have attracted investments from Asian manufacturers like CATL and LG Chem, who have set up factories to supply the European market.
Their proximity to Germany, a key automotive production centre, along with lower land and labour costs, has made Eastern Europe an attractive destination for investors.
Meanwhile, David Santiago, CEO of TERA Batteries Recycling, notes that Spain also holds significant potential in this market.
“Spain has been a leader in car manufacturing for years… it is capable not only of producing but also of leading the value chain of electric mobility,” explains Santiago.
Its established infrastructure and proximity to vehicle manufacturers give it a strategic advantage in cell production.