On December 21, the Council approved a proposal to grant automotive manufacturers in the European Union (EU) and the United Kingdom (UK) more time to meet local content requirements for electric vehicles (EVs) and batteries under the Trade and Cooperation Agreement between both regions.
By extending the current rules of origin until December 31, 2026, it will prevent stricter regulations from coming into effect on January 1, 2024, and a 10% tariff will not be applied to products traded between the EU and UK that do not meet these requirements.
However, this decision poses a challenge for the sector, as the industry is expected to adapt to more stringent local content requirements by 2027 through an increase in the production of EV batteries during this period.
To this end, support of approximately 3 billion euros will be provided from the Innovation Fund.
It is worth mentioning that the reason for the Commission’s proposed extension was that it believed the battery industry could not take off as quickly as anticipated.
While this decision is presented as a “victory” for the sector, the battery industry must now increase its production capacity at an appropriate pace to meet the forecasted demand.
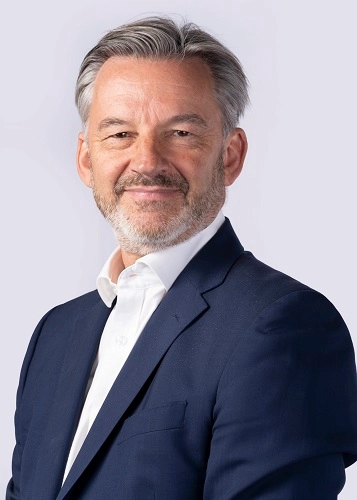
“With significant investment committed to UK automotive manufacturing, production volumes increasing and the imminent threat of tariffs on EVs traded with the EU now removed by the extension of current rules of origin until 2027, there is renewed confidence in the sector,” says Mike Hawes, Chief Executive Officer at the Society of Motor Manufacturers and Trades (SMM).
“We now need to see the Anglo-European battery industry build capacity at pace to meet forecast demand,” he adds.
Studies indicate that the market demand for these electric packs will skyrocket from around 800 GWh in 2022 to 4,900 GWh in 2030, thanks to the electromobility revolution and the transition to green energy.
Furthermore, it is expected that EVs will represent around 80% of the demand for lithium-ion batteries in the coming decades.
In this regard, stakeholders must act quickly to ensure the supply of raw materials.
But is the European industry prepared to navigate the complexities and balance the supply and demand?
The Battery Monitor report, prepared by Roland Berger in collaboration with the PEM group at RWTH Aachen University, outlines the challenges facing the sector and the measures that need to be considered.
Firstly, it’s important to note that while new regulations on batteries, including goals for recycled content and rules on carbon footprint disclosure, were adopted in Europe, the United States introduced an Inflation Reduction Act (IRA).
The document details that “the IRA is shaking up the battery market, and now the United States is much more attractive to investors than Europe.”
Implemented last year by the Joe Biden administration, the IRA is a measure endowed with $369 billion to incentivize green industrial initiatives, including gigafactories.
As a result, European organizations like Transport & Environment (T&E) reported that lithium battery manufacturing projects in Europe were at risk.
Specifically, they indicated that 68% of them were at “high or medium” risk of being interrupted or lost.
However, the EU approved a sustainable investment framework known as IPCEI (Important Project of Common European Interest), which is considered a response to the USA’s IRA.
Therefore, despite the challenges facing the European industry, various factory installation projects have emerged.
It is even anticipated that, while many consider this to be utopian, Europe will have 250 new lithium-ion battery plants in the next 10 years, according to a report by Buck Consultants International.
“As there is a substantial disconnect between Europe’s electric vehicles ambitions and current batteries manufacturing capacity, we expect a wave of new plants,” says René Buck, CEO of Buck Consultants International.
“Not only from the battery manufacturers themselves like CATL, BYD, LG, and Panasonic – but also from their suppliers, the producers of for example anodes, cathodes, separators, and battery management systems,” he adds.
As of the present date, plans have already been revealed in France, Germany, Hungary, Italy, Norway, Poland, Spain, and the United Kingdom for the coming years by companies such as LG, SK Innovation, and Samsung.
In France, in the city of Douai, the Chinese company Envision will invest up to 2 billion euros in a gigafactory for Automotive Energy Supply Corporation (AESC) near the Renault ElectriCity electric vehicle production center.
In Dunkirk, the Taiwanese company ProLogium is working with the French government to secure grants for a 5.2 billion euros factory, with production expected to commence in 2026.
In the same city, the French company Verkor plans to build a plant with a capacity of 12 GWh, with Renault as its main customer.
Germany has high expectations for the coming years. The Swedish company Northvolt will invest between 3 billion and 5 billion euros if a currently under-review grant for a factory in Heide is approved.
In Kaiserslautern, Automotive Cells Company (ACC) plans to open a gigafactory as part of an initiative involving multiple facilities across the continent, supported by Saft-TotalEnergies, Stellantis (PSA-Opel), and Mercedes.
Also, although details are limited, the German company CellForce is set to inaugurate a factory in Tuningen by 2024.
Volkswagen has an ambitious local project, aiming to open six plants across the continent by 2030. The first is scheduled to begin operations in Salzgitter in 2025.
Finally, the Chinese company Svolt will allocate up to 2 billion euros to open two facilities, one in Überherrn and another in Lauchhammer, both expected to be operational by the end of 2025.
In Italy, the local company Italvolt is ready to inaugurate its 3.5 billion euros factory in 2024.
Another local competitor, FAAM, with an investment of 570 million euros, expects its plant in Teverola to start operating in 2024. ACC also plans to open a facility in Termoli in 2026.
In Norway, the national company Freyr invested 1.7 billion euros to open a state-of-the-art factory in Mo i Rana, expected to be operational by 2028.
Morrow expects the first of four stages of expansion of its 470 million euros plant in Arendal to begin operating in 2024.
Additionally, Beyonder has chosen Haugaland to inaugurate its factory next year.
Another Scandinavian company with significant projects is Elinor, which invested around a billion euros in a plant expected to be operational by 2026.
In Spain, BASQUEVOLT plans to invest over 700 million euros in a facility, aiming to produce 10 GWh by 2027.
Concurrently, the Spanish government signed an agreement in July 2022 with the Chinese company Envision to build a 2.5 billion euros factory in Navalmoral de la Mata.
At the same time, Volkswagen and its partners announced in 2022 that they will invest 10 billion euros in a 40 GWh plant, with production starting in 2026.
Another announcement in 2022 was from InoBat, which signed an agreement with the Spanish government to establish a 32 GWh factory valued at 3 billion euros.
Regarding the United Kingdom, Coventry has approved a site for a potential facility, but an investor has not been found yet.
On the other hand, the Indian group Tata will build a gigafactory worth 4 billion pounds in Somerset to supply its Jaguar Land Rover factories, expected to start operating in 2026.
Additionally, Envision is back in the spotlight with the construction of a gigafactory in Sunderland, set to be operational in 2025.
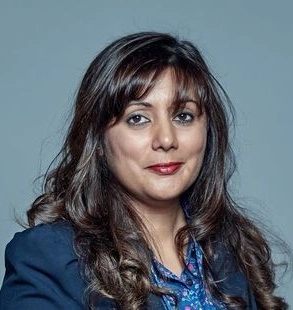
Finally, it’s worth noting that the UK government is considering seven sites for a plant with an investment from NanoTech Energy, which has allocated a billion pounds.
In late November, the UK launched its battery strategy with the goal of becoming a globally competitive industry in design and development.
“Batteries will play an essential role in our energy transition and our ability to successfully achieve the net-zero emissions target for 2050,” stated Nusrat Ghani, Minister of State for Industry and Economy.
Ghani emphasized the action of allocating over 2 billion pounds to research and development (R&D) and supporting the manufacturing and progress of zero-emission vehicles, their batteries, and the supply chain over five years.
Other challenges for the battery industry: raw material supply
The increasing demand for batteries, driven by the rise of EVs, puts pressure on the availability of raw materials.
In this regard, the focus is now on securing the supply of materials, improving production technologies, and exploring alternatives to lithium-ion cells.
For instance, producers are seeking to ensure supply through partnerships and agreements with miners and new lithium production technologies, such as direct extraction.
Moreover, the Battery Monitor suggests that the EU should support raw material supply “by entering into free trade agreements with countries like Australia, Indonesia, and Argentina.”
It’s worth noting that the International Monetary Fund (IMF) recently issued a report anticipating a significant increase in the demand for essential minerals for electric vehicle batteries by 2030.
According to the report, the demand for lithium will multiply by six, while copper will increase by 1.5.
Additionally, it is estimated that the demand for nickel and cobalt will double over the same period.
This growth could equate the importance of these minerals to crude oil for the global economy in the next two decades, significantly impacting the prices of these resources.
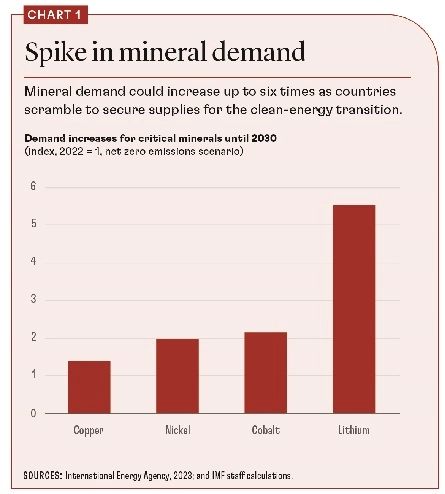
However, according to a Goldman Sachs study, battery prices are expected to drop to $99 per kilowatt-hour (kWh) of storage capacity by 2025, a 40% decrease from 2022.
Analysts believe that this will largely occur due to the decrease in raw material prices for EVs, such as lithium, nickel, and cobalt.
Thus, it is expected that battery pack prices will decrease by an average of 11% annually from 2023 to 2030.
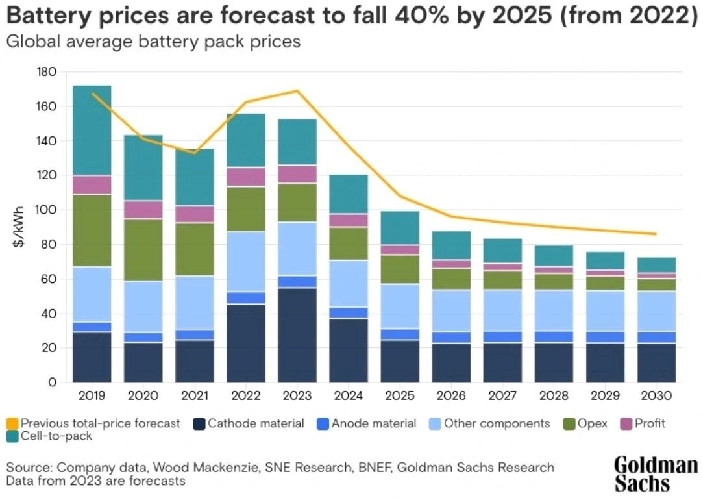
This price drop would have a positive effect on the development of more affordable electric vehicles.
Read more: European companies announce EVs for less than €25,000. An assured destination?
As the study explains, the trend in prices is downward, driven by three factors.
Firstly, it is due to the clearance of battery mineral prices as more mines and processing centers come online.
Secondly, new chemistries like lithium iron phosphate (LFP) and sodium-ion, made from highly abundant minerals, are drastically reducing costs.
Lastly, it is attributed to new packaging and cell technologies aimed at cost reduction.